When we see children laughing and sliding down a colorful slide in a park, it’s easy to forget how much thought and craftsmanship go into making that piece of equipment safe, durable, and fun. As a professional children’s slide manufacturer and non-powered amusement equipment supplier, we believe that transparency builds trust — and that every great play experience starts with a great production process.
In this blog, we’ll walk you through the step-by-step production process of a high-quality outdoor playground slide, from design concept to final delivery.
1. Design and Planning
Every slide starts with a concept. Our design team collaborates closely with clients to understand the project’s needs — including age groups, space requirements, safety regulations, and themes. Using 3D modeling software, we create a virtual layout of the slide structure to ensure functionality and safety.
✅ custom children’s slide design
✅outdoor playground slide manufacturing process
2. Material Selection
Choosing the right materials is critical for safety, longevity, and environmental impact. We typically use high-quality rotomolded polyethylene for plastic components and galvanized steel or aluminum alloy for support frames. All materials are tested for UV resistance, weather durability, and non-toxicity.
✅ high-quality playground slide materials
✅ UV-resistant non-powered play equipment
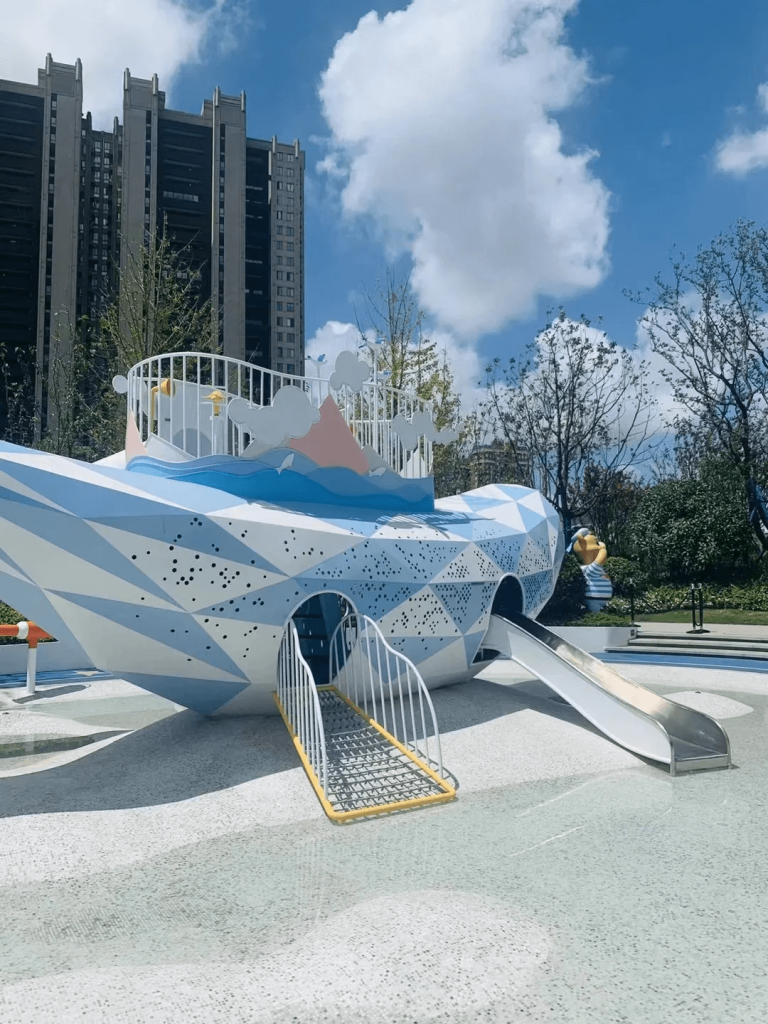
3. Mold Creation and Shaping
For plastic slides, we use rotational molding (rotomolding) — a process where plastic powder is heated and spun inside a mold to form hollow, strong, seamless parts. For metal components, laser cutting, welding, and bending are performed with precision to meet exact design specs.
✅ rotational molded playground slides
✅ seamless plastic slide manufacturing process
4. Surface Treatment and Finishing
After shaping, each component is carefully polished and coated. Metal parts undergo powder coating or hot-dip galvanization to prevent rust and corrosion. Plastic parts are trimmed, sanded, and sometimes painted with bright, child-safe colors.
✅ powder-coated playground structures
✅ corrosion-resistant outdoor slide equipment
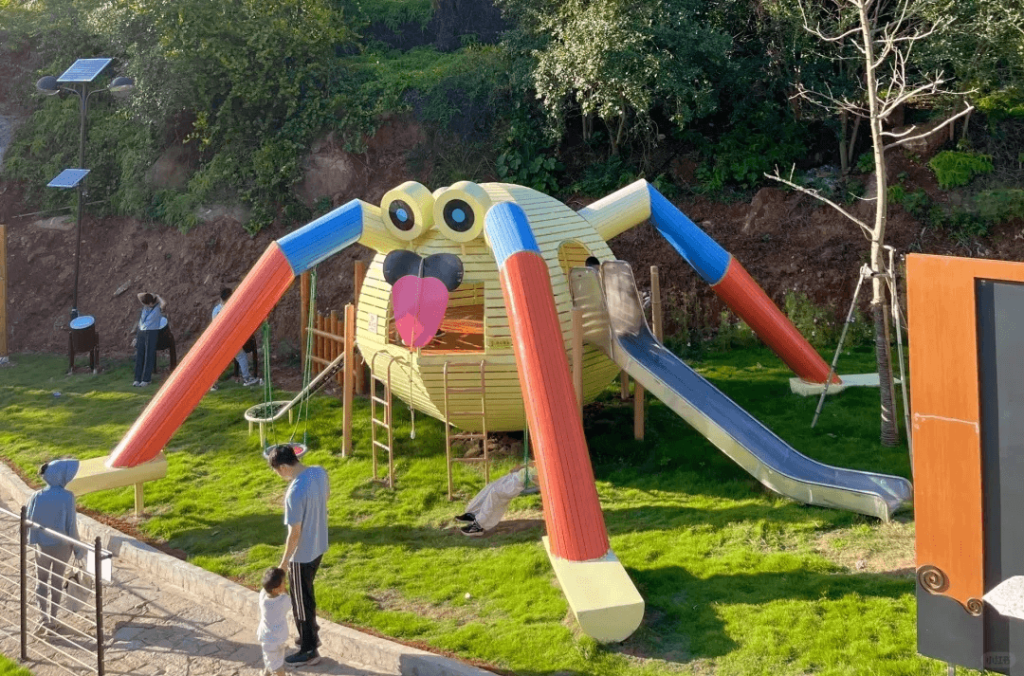
5. Quality Control and Safety Testing
We run multiple quality control checks to ensure that every piece meets national and international safety standards (such as EN1176, ASTM F1487, etc.). Slides are tested for weight limits, edge smoothness, anti-slip surfaces, and structural stability.
✅ certified children’s slide manufacturer
✅ playground equipment safety testing procedures
6. Assembly and Pre-Installation Checks
Before shipping, all parts are pre-assembled in our factory to confirm fit and function. This also allows us to minimize installation errors at the site. Any moving parts or joints are double-checked for alignment and performance.
✅ pre-assembled playground slides
✅ non-powered slide installation support
7. Packaging and Delivery
Finally, the slide components are carefully packed with protective materials to avoid damage during transit. We include detailed installation instructions or offer on-site support, depending on the client’s needs.
✅ slide equipment packaging and delivery
✅ international shipping for playground slides
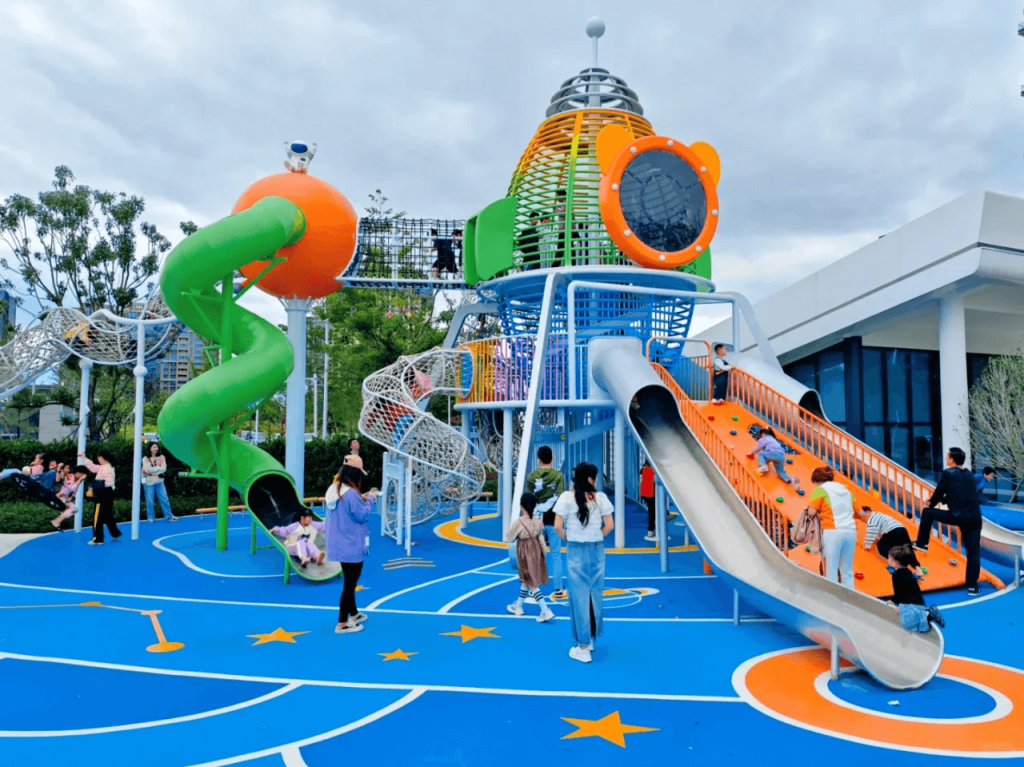
Final Thoughts
Making a safe and engaging children’s slide isn’t just about bending metal or shaping plastic. It’s about understanding how children play, how weather affects materials, and how safety must be built into every joint, curve, and corner. As a professional non-powered amusement equipment manufacturer, we take pride in every piece we create — because we know it’s not just equipment. It’s a childhood memory in the making.
If you’re looking for a reliable partner for your park or playground project, feel free to reach out to us. We offer custom designs, high-quality manufacturing, and expert support every step of the way.